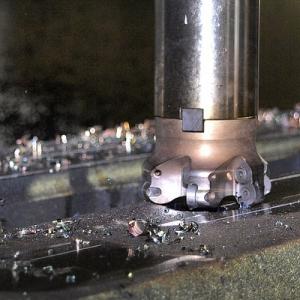
Improving Efficiency in Industrial Manufacturing
Simplifying Report Generation for High-Mix, Low-Volume Industrial Servo Valve Tests
Client: A major industrial servo valve manufacturer
Challenge
A manufacturer of components for both commercial and military aircraft built a large number of different models of servo valves. Some models were made only a few times each year, while other models were made with an order of magnitude higher volume. Each unit underwent rigorous testing during and after assembly.
Our client needed to submit the results of that testing to their customers but since the production and testing of each unit happened in many locations, possibly even around the world, many hours were spent locating the appropriate datasets and assembling the report.
Furthermore, our client wanted to improve their responsiveness to requests from their customers by having rapid retrieval of the test report for any part after it had been delivered into the field.
Solution
Since the test datasets were varied due to the large numbers of different valve models and associated test procedures, a database was created using a platform based on the Resource Description Framework (RDF). An RDF database can accept arbitrary types of data, manage that data through metadata tags, and adjust gracefully to changes in content and shape of the connections between objects in the database.
This adaptability was key to our client being able to leap past some of the issues in standard SQL-based relational databases.
The results from each test run on each part at each (PXI-based) test system were tagged with metadata and pushed into the RDF database. The StepWise test executive platform interfaced to the RDF database by outputting XML content which was scanned by a routine created for the RDF database and converted into the RDF data and links. The part ID was a critical tag since this allowed searching the RDF database for all results associated with that specific part. This database resided on a server at the client’s headquarters and accepted data from worldwide locations.
Once the data for each part was housed in the database, a report could be generated. To accommodate the variety of data in that report, web technology was used to render the report pages based on the types of data entered into the database, as described by the metadata tags. For example, data identified as waveforms could be plotted or listed in tabular format. Having reports rendered based on the data types made it possible to handle adjustments to the types of data measured by the test system.
Results
With the ability to render reports quickly, our client could produce detailed reports for their customers indicating the performance of any specific requested servo valve.
Our client was able to trim the time to create reports to less than 1 day from the previous effort of 3-5 days and with less error.
- Data are now organized uniformly, simplifying the location of desired information, as compared with files stored on various test PCs and file servers.
- The client has the ability to generate automatic emails to their customers with the required reports already attached and ready to go.
- In potential warranty and customer service situations, having the ability to send the customer a report within hours represented great customer service.
All these features are available consistently across worldwide manufacturing facilities, reducing training and maintenance of procedures. And, of course, the reports handle using metric or English units as appropriate for the end customer.