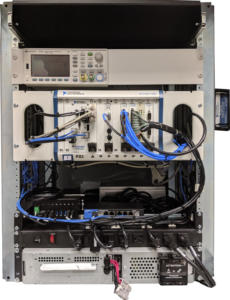
What should I keep in mind when I’m launching a new product and considering a custom manufacturing test system?
I need solid traceability. What are some ways to accomplish this?
There are at least two parts to this.
First, measurements require calibration traceability. Test system calibration is accomplished either by having all components of the test system, such as sensors and actuators, data acquisition and measurement equipment, calibrated individually to NIST-traceable standards. The overall accuracy of the system is then traceable to NIST. The other method to perform system calibration looks at the entire system as the device to calibrate. This method is more precise, since individual accuracy errors don’t stack up, but typically harder since the traceable calibration equipment needs to be brought to the test system rather than the other way around as done with the individual components.
Second, results often require traceability to the part. If the part has a unique serial number or ID, then tag any results, whether measurements, calculations, timestamps, and so on, with that number. Any future questions about the part can be traced to that part’s historical data. Here’s an example of a test executive that enables part traceability.
What if I need to increase throughput after launch? Are there things to think about ahead of time to plan for this possibility?
Not generally. If you designed your system to run faster that you are operating it, then why aren’t you operating it at maximum speed? The only way to increase throughput is to add more hardware.
One method is to duplicate the test system to double the capacity. Watch for issues with consumption of any plant facilities during this duplication, such as shop air or electrical power. For example, running two systems on the same shop air might cause the air pressure to drop enough that the pneumatics no longer operate as expected.
Another method adds more hardware to the existing test system and has the controller and/or PC run additional test applications in parallel, watching for resource constraints on any shared resources, such as that one super expensive oscilloscope that you chose not to duplicate.
My customer and management would really like better reports on test results, but creating reports in the past has been painful. What can I do to make this easier?
If you need the test report to travel with the part as hard copy, then consider utilizing general-purpose results objects, such as graphs, tables, images, and text and then be disciplined to utilize only these objects. Any report that can’t be fulfilled with these objects is a deviation and is not acceptable. Viewpoint often creates reports in HTML for viewing and rendering. The formatting is often not “pretty”, but it’s functional and reusable and fast to create once you have the tools in place.
If electronic records are acceptable, then you can either:
- use the same methods as with the hardcopy method above except with the results in a file or
- push basic results to a database and/or file folders for subsequent rendering with a tool that interacts with the database.
There are many tools that are better at rendering reports than raw LabVIEW or C#. But these are often better used with electronic records.
Perhaps the biggest challenge with reports is consistency. If you must create new reports for every product type and with every customer, then that’s a lot of work no matter what tool is used. Strive for consistency even if you must convince your customers that the results will look different than they saw before.
I’ve got a pretty manual assembly process. I’d like the test system to be interactive with the operator, not just for test but for assembly as well. What should I be thinking about?
- Convert any work instructions into an electronic document in a step-to-step translation.
- Present each step to the operator as a step in a test sequence. The test sequence can drive operator consistency by presenting assembly steps in a known sequence, with acknowledgement by the operator upon completion of the step before the next one is presented.
- The test step can gather any measurements that might be needed for a specific assembly or assessment step.
Next Steps
Want someone to take the manufacturing test system off your plate? Reach out to start a conversation. Want to see some manufacturing test system case studies? See here.
Deep into learning mode? Check out these resources:
- NI Hardware Compatibility – real-world tips and lessons learned
- How to prepare for when your test team starts to retire
- Practical manufacturing test and assembly improvements with I4.0 digitalization
- What to do with your manufacturing test data after you collect it
- 5 Keys to Upgrading Obsolete Manufacturing Test Systems
- How Aerospace and Defense Manufacturers Can Make the Assembly and Test Process a Competitive Advantage
- 9 Considerations Before you Outsource your Custom Test Equipment Development
- Reduce Manufacturing Costs Report
- Improving Manufacturing Test Stations – Test Systems as Lean Manufacturing Enablers To Reduce Errors & Waste