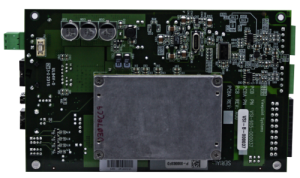
Industrial Embedded Equipment – Leak Tester
Shortened Product Development Cycle for Industrial Equipment – A Leak Tester
Background
Leak testing sounds simple. It seems like all you have to do is wait for the pressure (or vacuum) to drop by a detectable amount and estimate the leak rate based on the time it takes to reach that detected decrease. But, in an assembly line, it’s not, mostly due to the desire to do everything as quickly as possible.
Many manufactured products need to be tested for leaks to be sure they hold pressure or vacuum. Examples are fuel cells, braking systems, air bags, air conditioner components, balloon catheters, and so on. The list is almost endless.
Our client needed to develop a new leak tester with lower cost and more sensitivity and same small size.
Technical Highlights
The manufacturer wants the test to run as fast as possible – production volumes can’t tolerate a long wait to sense a leak. And, don’t forget, these products are not supposed to leak, so the “bad” ones leak very s-l-o-w-l-y. This is where the complexity in performing a leak test in a manufacturing environment arises.
The tester must be super-sensitive – to be able to sense a leak as soon as possible balanced by cost constraints and the need for the tester to be physically small so it fits on the production line
The tester needs to provide a solid user experience – so it needs to be robust and smart so the production test operator can just use it without hassle.
Challenges
Our client had been building commercial leak testers for many years. Their development tools were built on in-house hardware designs and a software library for making measurements and interacting with the operator via buttons and a display.
The typical development cycle extended to over 1 year and they wanted to shorten that development timeline by utilizing more Commercial Off The Shelf (COTS) components, especially since embedded controllers had improved dramatically over the recent years, and they did not sell a huge number of these specialized product per year. Put another way, they were looking for a supplier that would pay better attention to them since they were competing for responsiveness from say the microcontroller vendors when those vendors were used to customers purchasing 100s of thousands of microcontroller per year. They were ready for a change in design tools and subcomponent vendors.
Another issue was the need for extremely accurate pressure detection (so the leak test could be fast!). They wanted to go with COTS components, but they could not find a COTS detection system (sensor and digitizer combination) with enough accuracy and responsiveness. They needed a hybrid approach of COTS for the controller and custom for the signal conditioning and acquisition I/O.
Results
The prototype unit was designed, built, and ready for testing of the leak testing capability in about 2 months after the requirements were completed. The collapsed single-board solution was then designed, built, and unit tested about 1 ½ months later.
Leak Tester Sub-assembly and enclosure
The custom circuitry combined with some proprietary algorithms executed on the NI SOM RIO was able to measure with about 10 times better sensitivity than the previous generations. This sensitivity translated into faster leak measurement times – a real selling point to our customer’s customers.
The customer was ready to do their validation in about 4 months after we had the green light to build. The ready-to-go VERDI prototyping system was a huge time-saver.
Viewpoint’s Solution
We worked with our client to develop a system based on the NI RIO platform from National Instruments (NI). We initially considered the NI sbRIO but chose the NI SOM RIO (sbRIO-9651) because of its size and slightly lower costs.
NI SOM
After an initial review of the customer’s design goals and requirements, a concerted effort was spent to morph those goals and adjust those requirements by iterative discussion between both of our engineering teams. It was truly a collaborative requirements gathering and design activity. We brought our knowledge of the NI SOM RIO I/O and LabVIEW programmability capabilities and the customer shared their understanding of leak detection and their customer needs.
VERDI – Chassis with modules
Enter VERDI – Once the requirements and initial design were complete, we designed and built a custom A/D and signal conditioning circuit board that could interface with the NI SOM RIO. The initial version of this board was designed to connect to our VERDI prototyping system so we could rapidly validate the performance of the circuitry without needing to build the complete single-board system (with SOM and other circuitry all on one board).
After some tweaking to improve this custom circuitry, we essentially copied the board layout from all the necessary I/O (SOM controller board, digital I/O, display I/O, and the custom leak-detection circuitry onto a single-board system. This effort was reduced, since we had a large amount of ready-to-reuse hardware designs already developed for the VERDI prototyping system.