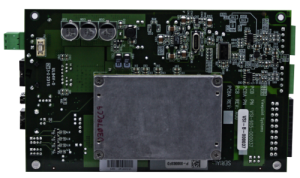
Reduce Development Cost and Risk with a SOM-based approach for Industrial Embedded Designs
One of the biggest ways to reduce engineering development costs and risk is by utilizing existing hardware and software whenever possible
You’ve got a great idea for a new smart industrial machine, instrument, or piece of equipment that you think has a good chance of doing well in your industry (okay, maybe it’s not as sexy as designing the Model S or the new iPhone, but in your world, this is a pretty cool idea you’ve got). You know you’re on to something because you’ve lived in your domain long enough to recognize real pain when you see it.
Now you need to actually make the thing. You’ve talked to some people you know that you think fit your target customer profile wonderfully. You get them all excited, a few of them excited enough to actually give you some money to be early adopters and try the thing out. Now the race is on. You know it’s important to be successful out of the gate. You don’t have a ton of time, and you sure didn’t get enough money to plan for 10 years down the road. You need to bootstrap yourself and get the thing out the door yesterday!
Maybe you have a pretty good handle on the mechanical aspects, the algorithms, and the sensors, but you either don’t have the background, or maybe you just don’t have the manpower, to tackle the embedded electronics hardware and software.
Read on to learn how you can reduce engineering costs (AKA non-recurring engineering or NRE) and development risks with a SOM-based approach for your industrial embedded system.
Embedded System Value Layers
One way to talk about your embedded design is in terms of value layers, like in this diagram:
At the core layer you’ve got the core processing, memory, and communication interface elements. Layer 1 includes things like the application software and custom electronics, and then layer 2 includes the final packaging and integration. A more detailed visual would look something like:
One of the biggest ways to reduce engineering development costs and risk is by utilizing existing hardware and software whenever possible.
Of course if some performance criteria can’t be met with something off-the-shelf, you have no choice but to utilize a custom component to satisfy that requirement. But whenever possible, you want to re-use what’s already been developed because that cost is likely being amortized, and existing components have already been validated.
The main potential candidates for re-use in a scenario like this are:
- Processor – absolutely. Many processors are architected for a variety of applications. In addition, if you can re-use many of the support components you put down onto a circuit board, then you get that re-use as well.
- Memory – absolutely. A similar story applies as for the processor.
- Communication Interfaces – in many cases, yes. While different applications do call for different communication interfaces, there are a handful of very popular interfaces for different applications, including Ethernet, USB, CAN, I2C, SPI, and RS-232/485/422.
- I/O Hardware – Many industrial applications follow the 80-20 rule whereby 80% of applications are satisfied by some common I/O, such as analog outputs (e.g. +/- 10 V or 4-20 mA) with a maximum of few 10s of kHz sampling rate, thermocouples, digital I/O (e.g. 3.3V or 5V), and some sensors needing excitation (e.g. bridge-style or IEPE). After a few projects, a set of I/O circuitry built for other projects can be reused for new projects.
- I/O Firmware – this is generally going to be tied pretty directly to your chosen I/O hardware, so depending on how much you can re-use your I/O hardware will mostly drive your ability to re-use your I/O firmware. On top of that, some serial interfaces are pretty prevalent, for example SPI, so that firmware has a high probability of re-use across different hardware.
- Power Regulation – this is very dependent on the various ICs that you need for your application, but there are certainly ways to increase re-use here.
- Application Software – much of this is going to be specific to your application, essentially by design. There still may be some potential areas for re-use with core functional blocks for things like PID loops and FFTs.
- Packaging – this is another area that will mostly be unique to your design.
Based on this assessment, we’ll leave packaging and application software alone, since they aren’t usually the best candidates for re-use, and group the remaining items into two categories:
- Core Hardware – memory, processor, and some of the communication interface elements.
- I/O – we’re going to include I/O hardware and firmware in this category, as well as some additional communication interface elements. We’ll also lump power regulation into this category for now, even though it doesn’t quite fit, since our I/O (and core HW) will require power supply regulation.
Development Cost and Risk Reduction Category 1 – Core Hardware
The controller market offers a core hardware sub-assembly concept known as a System On Module (or SoM). There are several SoMs out there from various vendors. One of them is made by National Instruments. The NI SOM hardware (the NI sbRIO-9651 SOM) consists of the bare necessities to act as the core hardware element, including a processor, memory, some communication interface foundational elements, and an expansion connector to be able to connect your I/O to. The processor is a Xilinx Zynq SoC, which is a pretty awesome little chip, incorporating both an FPGA and a dual-core ARM-based processor in a single silicon package. Check out the Zynq-7000 devices here.
For more details on the NI SOM, check this out.
Development Cost and Risk Reduction Category 2 – I/O
Since you’re developing an industrial embedded machine, instrument, or piece of equipment, then chances are, you need to interface to something, so you’re going to need I/O. You might need analog inputs to monitor temperature, pressure, or vibration, or you may need 5V outputs or a serial interface to control a valve or actuator. Maybe you need GPS for position or timing information, or maybe you need to send data off to the cloud via Ethernet.
At Viewpoint we’ve taken some of the more common I/O and created modules out of them (some hardware, some firmware, and some both), and created a platform called VERDI to help with your I/O needs. Check out the VERDI modules here. If you need a module that we don’t have in our holster, we can design it for you.
Next Steps
Hopefully this article has provided a path for you to continue to make progress with your industrial embedded system. If you want to see if VERDI is a good fit for your application, request a demo. If you’re interested in more useful info on industrial embedded systems, check out our resources page.