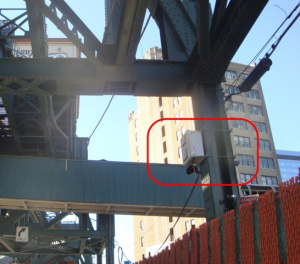
Industrial Embedded Monitoring – Remote Structural Health Monitoring
Using a cRIO to remotely assess structural health
By connecting these systems with a host PC, we can monitor continuous vibration activity and alarm conditions on a variety of structures despite inclement weather.
Challenge
Continuously monitoring the structural health of the Long Island Railroad (LIRR) Viaduct despite the relative inaccessibility of the structure.
Solution
Using CompactRIO, LabVIEW FPGA, and the LabVIEW Digital Filter Design Toolkit to measure the modal analysis of vibration data generated from ambient excitation, capture this data remotely, and analyze significant events.
Background
Engineers use structural vibrations to assess the conditions of many constructions and machines, including buildings, bridges, dams, towers, cranes, and mountings. Although we have had tools to monitor structural vibration for decades, these tools restrict data collection to short durations of high-fidelity waveforms or longer durations of summarized power in frequency band results. Many structures vibrate in meaningful ways only in the presence of ambient forces such as wind, vehicle activity, nearby construction, or random events such as earthquakes and tornados. Therefore, data collection needs to be active during these events.
Due to recent improvements in memory storage, processor speed, and wideband wireless communications technology, we can collect high-fidelity waveforms over long periods. We can also communicate to host PCs that aggregate structural vibration data across multiple collection locations, providing permanent data collection and superior analysis and reporting capabilities.
STRAAM Corporation, a leader in structural integrity assessment, and Viewpoint Systems, a Select National Instruments Alliance Partner, collaborated to develop a system that functions outdoors and in other less-accessible sites and maintains the capabilities of the available PC-based solution. Ultimately, we produced an enhanced version of STRAAM’s SKG CMS™ system to install on a Long Island railroad bridge.
System Requirements
The system needed to perform the following operations:
- Collect data from accelerometers and other environmental sensors
- Store weeks of data locally at full acquisition rates
- Analyze custom data in real time
- Publish summary statistics periodically to the host
- Upload waveforms to host on request
- Offer rugged, lightweight, cost-effective, reliable OEM deployment
- Contain flexible architecture to handle future capabilities
- Ensure secure user access control
System Design
We chose a system based on the NI CompactRIO platform and dynamic signal acquisition (DSA) C Series modules. The CompactRIO and associated C Series signal conditioning modules have an operating temperature range of -40 to 70 °C, well within typical environmental extremes for most installation locations. Additionally, the CompactRIO controller has no moving parts, increasing the mean time between failure and ensuring it can withstand physical mishandling during shipment and installation. For software, we decided to use the NI LabVIEW Real-Time Module and the LabVIEW FPGA Module. We used LabVIEW FPGA for basic signal acquisition as well as some custom antialiasing filtering to allow for sampling rates below the capabilities of the DSA module.
Figure 1 – Equipment mounted to LIRR Support Beam
Data Acquisition and Filtering
The DSA module acquired acceleration signals via special sensors, supplied by STRAAM, that output information about tilt and acceleration. Because large structures resonate at low frequencies, it is important that these sensors have extremely low noise, high dynamic range, and low frequency response to gather information about structures at less than 1 Hz. The low frequency range and long-term data storage need combine to create a maximum data collection rate frequency of 200 samples per second (S/s). The NI 9239 does not sample that slowly due to its delta-sigma converter technology, so we sampled at 2,000 S/s and used lowpass digital filtering on the field-programmable gate array (FPGA) to produce an antialiased signal at 200 S/s. Simple subsampling through decimation would violate the Nyquist criterion. Using the LabVIEW Digital Filter Design Toolkit, we produced a 28-tap infinite impulse response (IIR) filter with a 3 dB roll-off at 0.8 times the sample rate with a stopband attenuation greater than 90 dB. The Digital Filter Design Toolkit includes tools to automatically generate code to deploy the filter to the FPGA. We carefully selected fixed-point arithmetic to ensure proper operation without using excessive FPGA resources. The final filter was a 24-bit fixed-point solution with a 4-bit mantissa.
Figure 2: Remote Front Panel Displaying Acceleration Waveform Capture
Configuration, Signal Processing, and Alerts
STRAAM uses proprietary analysis routines, based on the structure’s resonant frequencies, to extract relevant information from the continuous stream of acceleration data. Because ambient energy excites the structures, we analyzed some initial data to locate these resonances. After this initial period, we configured the CompactRIO to perform the proprietary analyses based on the location of these resonances. We handled all activity in this initial setup remotely via wireless communications. We connect to CompactRIO over a wireless connection, then to a LabVIEW remote panel where we initially acquire and assign resonance bands.
The signal processing requires the spectral power and time-domain structure of the waveforms inside those resonant bands. The CompactRIO processor and FPGA module can calculate fast Fourier transform (FFT)-based power spectrums and perform time-domain filtering calculation so we can base calculations on the complicated algorithms provided by STRAAM. Furthermore, the large CompactRIO RAM can archive raw acceleration waveforms for later retrieval. The LabVIEW development environment greatly simplifies adjusting these calculations. We apply additional calculations to identify noteworthy events to alert the engineers when important conditions occur. These conditions may signify the presence of a meaningful ambient excitation or that considerable changes to the structure have occurred.
Host Communication
In order to successfully operate, this system needs to communicate effectively to the host PC. Because the system is deployed in almost-inaccessible and outdoor locations, all interactions with the system should occur remotely. Using cellular modems, the system connects via TCP/IP to upload important information, issue event alerts, and allow remote configuration. We designed the LabVIEW application to send periodic summary information via custom binary messages to the host with information about the condition of the structure and the CompactRIO system. The host then tallies this information along with all other SKG CMS™ systems deployed in the field. In addition to this summary information, the host can pull raw waveform data from the CompactRIO RAM. To avoid tampering and unauthorized access, we password protected all connections.
Figure 3 – Data File Configuration Screen
Summary
We have successfully installed several functional SKG CMS™ systems based on the CompactRIO platform. By connecting these systems with a host PC, we can monitor continuous vibration activity and alarm conditions on a variety of structures despite inclement weather. Our customers enjoy the benefits of modern Ethernet-driven, Web-based connectivity to verify the status of their structures and we enjoy the benefits of the rugged, reliable, low-cost, and reprogrammable CompactRIO system for data collection.