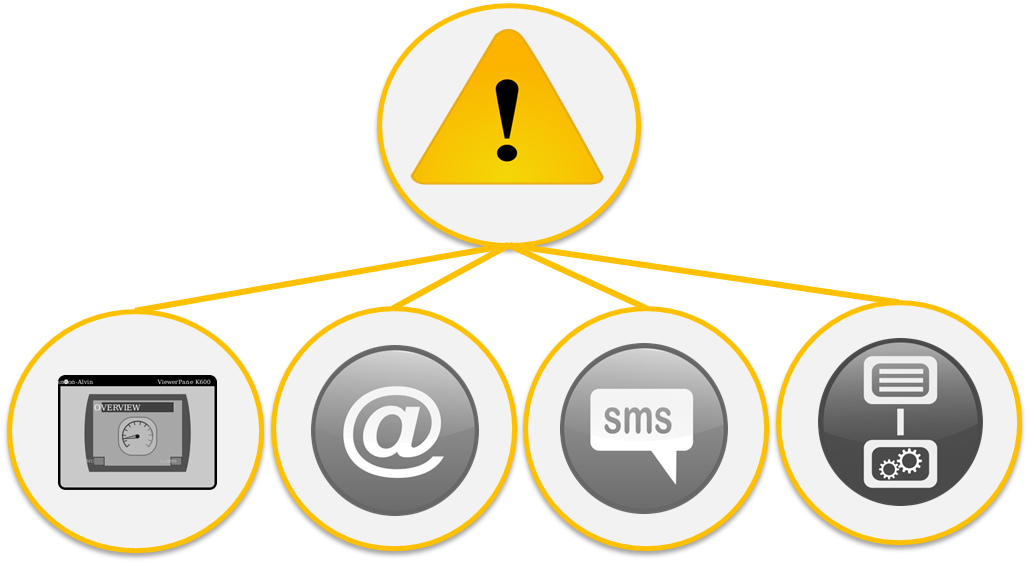
Online Condition Monitoring for OEMs – What Is It and How Can It Help Me?
From a functional perspective, it’s all about indicators and actions
The focus of this article is on small/medium-sized companies (those with less than 500 employees). It is geared toward companies in the industrial space (vs consumer), that manufacture systems or sub-systems (machines, equipment) that are generally more expensive (~$4,000 – $200,000 per unit), and have lower production volume (10’s – 1,000 units per year).
What is online condition monitoring (OCM)?
For the purposes of this article, we’ll define online condition monitoring as the continuous measurement of an asset in-situ to determine its state, generally with the end goal of reducing downtime, increasing efficiency, or reducing waste.
The asset could be an industrial machine (a pump, a generator, a manufacturing tool, etc.), or it could be a piece of infrastructure (a bridge, a pipeline, etc.).
What’s out of scope for this discussion?
- This discussion does not get into online condition monitoring for end users. That is, adding condition monitoring to assets that are used internally. There are many similarities, but they are not the same.
- We’re not getting into the business case for online condition monitoring here, although this is an important element of condition monitoring overall.
How can online CM help you?
We’re going to start with the end in mind. What is the objective with online CM? From a functional perspective, it’s all about indicators and actions.
Indicators:
Indicators include events and fault conditions, and inform you to take an action. These indicators are based on scenario-specific detection algorithms, and tie back to observable anomalies. They might provide indications directly or indirectly related to:
- Bad bearings
- Reduced power quality
- Motor efficiency
- Cracked blades
- Winding shorts.
The list goes on. Indicators could be displayed on a GUI, sent as an email or text message, or sent off to another machine.
Actions:
In response to these indicators, you want to be able to take some sort of action. Actions may include:
- Shut down a piece of equipment immediately.
- Check on or inspect a system further.
- Start collecting additional data for offline analysis.
- You might even use some of the information gathered to feed back into modifications for future product development.
Sometimes an action can be automated directly from one machine to another.
So how does this work?
Online condition monitoring functionally follows this sort of flow:
-
- You start with an asset you want to monitor. You have to observe some useful physical properties, so you have to instrument the asset with the right sensors and mount them in the right spot.
-
- Then, you have to measure that information. To do that, you may need amplification, filtering, or isolation stages prior to A/D conversion.
-
- Then, you process the raw digital data through a series of algorithms to detect good states vs. bad states. These turn into a series of indicators.
-
- Finally, you alert the appropriate people or other machines that something is not quite right and action should be taken.
Many scenarios focus on trying to determine if a system needs some sort of maintenance, but you should also consider condition monitoring for scenarios where you can automatically tune the system in order to maintain desired efficiency. For example, maybe you want to monitor the power factor on a power line where there are inductive motors being utilized (which can cause problems for neighboring sites), and instead of stopping at just monitoring, maybe you tune the system by dynamically adding in some capacitance to keep the power quality up.
Additionally, while much of the industry is focused on rotating equipment, CM can be applied to a much broader set of problems. For example, maybe you want to monitor the structural health of a bridge, or the condition of a pipeline.
The key is, if you can reliably detect the problem early enough, you may have a good candidate for online monitoring.
Where you might head from here:
If you’re ready to go deeper with online condition monitoring, check out this guide: Getting Started with Online Condition Monitoring – A Practical Guide for OEMs.
If you’re interested in taking a a step back and want to gain a better understanding of whether or not CM makes sense for your scenario, check out this white paper: Is Condition Monitoring Right For You? , where we’ll provide some basic answers to the following questions:
-
- When should I consider implementing condition monitoring?
- What types of physical properties can be sensed?
- What types of components can be monitored?
- What types of information can be produced?
- How do I translate the information into decisions?